It features an incremental washout unit (Plate Processor) with external punch and an automatic Dryer.
It is designed to washout and dry solvent-washable, polyester-backed, analogue and digital plates up to a size of 90 x 120 cm (36x48 inch) and thickness up to 7 mm (0.276 inches).
The standard version is equipped with a stress-accumulation early-warning-system and with tools to enable remote-monitoring and remote-diagnostics.
One of the most important feature of the Easy to Plate™ is the modularity concept, in other words, each unit is an independent piece of equipment buyable separately with the possibility of being upgrated and attached to one other to compose an all-in-one automatic unit.
This gives our customer 2 choices:
- buy the whole automatic line at once, or
- ammortize the investment and buy the different units over a longer time frame.
High efficiency
Less plates manipulation and manpower intervention for a higher quality: this also means a cost and time saving product. The risk of damaging a plate due to human intervention is virtually eliminated; as well as the inconvenience of direct contact with the solvent. In addition, the Easy to Plate™ has also a positive impact on the working environment: no more solvent smell in the workshops neither solvent leaks around due to dirty plates manipulation.
Full plate control
Another great advantage of the Easy to Plate™ system is represented by the set of internal cameras positioned to monitor the plate status after the washout section, as well as all the most sentitive mechanical transfer of the plate from one module to another. All the images captured by the cameras are displayed on the wide screen fixed to the dryer module and can also be seen and studied in remote by Vianord engineers. Each Easy to Plate™ is in fact equipped with a remote monitoring system, studied to assist the customer and follow up the unit status after installation. In addition to all this, a manual camera is also provided on every Easy to Plate™.
This allows the technician in loco to show in remote specific images to Vianord support team.
The Easy to Plate™ project encloses all the technological innovations in order to integrate all the steps of the photopolymer plates manufacturing in a all-in-one fully automatic line.
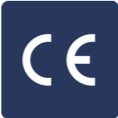
CE Certification
The equipment is designed and manufactured according to the EEC safety and health standards, as specified in the Type Examination Certificate No. MA19-0042548-01 (310) issued by IMQ spa – Via Quintiliano 43 – 20138 Milan ITALY, and on the basis of the verifications carried out according to the essential requirements of the Directive 2006/42/EC, the system respects and is in compliance with all the applicable points.

General Features
This fully automatic, PLC controlled, Easy to Plate System is specifically designed for high quality digital and conventional photopolymer plates for flexible packaging and flexo printing applications.

Modular
This is the first step towards the fully automated modular line. Composed by a processor (batch or incremental) equipped with a programmable automatic punching device and an automatic dryer.
One of the most important feature of the Easy to Plate™ is the modularity concept, in other words, each unit is an independent piece of equipment buyable separately with the possibility of being upgraded and attached to one other to compose an all-in-one automatic unit. This gives you two choices: buy the whole automatic line at once, or amortize the investment and buy the different units over a longer time frame.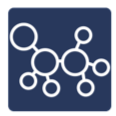
Solvent
It is designed to work in a standard “drum-to-drum” configuration where fresh solvent is supplied to the washout unit from a drum and the saturated dirty solvent is pumped from the unit to a recovery drum. It has been tested with conventional alternative solvents, with flashpoint above 62°C (144°F). The system's installation kit includes two Ø 16 mm - 5 mt solvent hoses with fittings, one level switch for the fresh solvent drum and another for the used solvent drum. Please note that if you intend to use this system with permanently installed tanks, special level switches may be required.
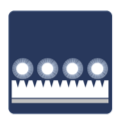
Processor

Dryer
- Drawers Pre-Heating management
- Temperature management system
- Separate Heat management (one each 2 drawers)
- Dedicated exhaust system
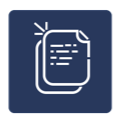
Production Data Recording

Stress-Accumulation Early-Warning

Remote Diagnostics
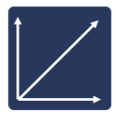
System Dimensions (net)
Washout Unit: 2280 x 1790 x 920 mm - (89.76 x 70.5 x 36.2”)
Exit Table: 1660 x 1790 x 920 mm - (84.33 x 70.5 x 36.2”)
Dryer: 1520 x 1790 x 1600 mm - (59.8 x 70.5 x 63”)
Total System: 5200 x 1790 x 1600 mm - (196.8 x 70.5 x 63”)
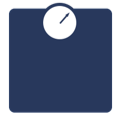
System Weight (net)
Exit Table: 450 Kg - (992 Ib)
Dryer: 1150 Kg - (2535 Ib)
Total System: 2650 Kg - (5842 lb)
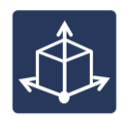
Packing Dimensions
Dimensions
Industrial Wooden Crates are favoured if the system must withstand multiple transhipments during transport and is mandatory when shipped outside the continent.
Dimensions
The dimensions mentioned above are for reference only; packaging dimensions may vary depending on the packing company hired for the job.
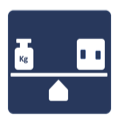
Packing Weight
The weights mentioned above are for reference only; packaging weight may vary depending on the packing company hired for the job.
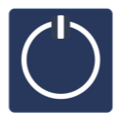
Mains Electricity
Power Supply (field configurable)
360 / 440 Volt – 50 / 60 Hz - 3Ph / N / PE - 207 / 243 Volt – 50 / 60 Hz - 3Ph / PE
Current (nominal load)
22 A (360/440 Volt configuration) - 38 A (207/243 Volt configuration)
Power Rating (nominal)
15.5 Kw
Connecting Wires
5 x 4 mm2 (360/440 Volt configuration) - 4 x 6 mm2 (207/243 Volt configuration)

Grounding
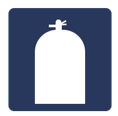
Compressed Air Supply
To perform to the best of its possibilities, the system requires a continuous and stable supply of compressed air at a pressure of at least 7 bar (101.5 psi) and not more than 10 bar (145 psi), with pressure dew point 3°C and max. residual intake oil content of < 0.01 mg/m3. Consider also an average consumption of 70 l/hr. The system installation kit includes a 5-meter - Ø 6mm air connecting pipe for push-in fitting.

Exhaust
The unit is equipped with a well-designed exhaust system that collect and conveys vapours and fumes from the different sections the machine and discharge them as quickly and silently as possible. The blower in the systems has sufficient power to vent the entire equipment when the tube supplied is connected directly to a vent hoods in the external wall or on the roof.
Duct connection
Washout Ø 140 mm (5.5”) Airflow: 600-650 m3/h
Dryer Ø 140 mm (5.5”) Airflow: 600-650 m3/h
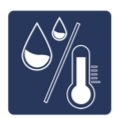
Working Environment
The system should be installed in a clean, constant-temperature and constant-humidity pre-printing environment with a temperature between 18 and 26°C (64.4 and 78.8°F) and a non-condensing relative humidity in the range of 40 to 60%.
To maintain such environmental standards an efficient heating/cooling and ventilating system may be required.

System Colour
Vianord offers all equipment in standard powder coating Vianord Black.
In addition, Vianord offers numerous ways you can personalize your system. In fact, Vianord offers the best customization options in the industry! This allows you to showcase your brand and company’s spirit in ways other companies can’t offer. You can choose your personal colour and have your logo, company name, or slogan pop.